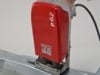
*This article appears in the July 2010 issue of Marking Industry Magazine
Quality: Traceability is a key to achieving quality. Those organizations with ISO: 9001 (or higher) certifications and that practice Lean Initiatives must use a variety of marking and identification tools to reach their goals.
Quality Management Using Direct Part Marking
Eight core principles of Quality Management guide organizations to look at the relationship with the customer, placing great value on their needs. The ultimate goal is to increase revenue and market share with a keen understanding that it can only be achieved thru enhanced customer satisfaction.
In order to achieve Principle 1 organizations are looking for strong leadership with vision that understand the need to evaluate and implement activities that motivate employees to meet ever increasing customer demands. Maximizing communication on all levels of their organization and providing people with the resources and tools to get the job done is the way to start.
Key to all organizations, and an often overlooked asset, are the people involved in making the goods and providing the services. Quality Management programs encourage innovation and creativity from their team members and at the same time hold them accountable for achieving the company goal of customer satisfaction. Encouragement to the team gets their buy-in to participate and looking for ways to improve the processes they are involved in.
Process improvements enable organizations to maintain and/or reduce costs while at the same time improving cycle times. Systems that have clear and defined instructions reduce error by operators, enabling them to interact with other departments smoothly to consistently deliver product on-time. Analyzing and evaluating the efficiency of the processes on a routine basis allows for identifying possibilities for improvement or eliminating processes that do not add value.
Structured systems that overlap and align processes between departments achieve optimum results keeping organizations focused on meeting the company goal – customer satisfaction. The dependency of each department on the other becomes an important part of the systems that utilize the resources to their fullest. Targeted and well-defined approaches to the activities in and between departments allow continual process improvement to occur and provide a means of evaluating the success.
Continual improvement is a self-reflection activity where you should ask why is this being done, why this way, is there another way that is better. Organizations that ask these questions are establishing a culture that seeks to improve the efficiency of the processes they are involved in reduce error and be flexible to react when needed.
Data resulting from process tracking allow the leaders within the organization to use facts to base their decisions. By carefully analyzing the data they are able to identify the cause and effect of situations that lead to process and/or system improvements. Communication and availability of the data is crucial to the decision process, allowing balanced, well-informed actions to be made swiftly.
While the majority of the quality management program involves the internal organization, the relationship with suppliers cannot be overlooked. Suppliers who practice quality programs themselves insure they will interact with the organization in a manner that meets quality management objectives. Evaluation of the supplier’s performance becomes part of quality management goals, holding the supplier accountable for providing quality products/services in smooth and timely transactions.
The evaluations organizations conduct to provide facts for process and system improvements for their quality management programs include details about operator error, machine failure and material defects. Each of these areas reflects justification for investment or corrective actions. Let’s look more closely at the manufacturing environment.
For organizations practicing Lean Initiatives, the production floor is setup in work cells. Within the work cells, you have material that is getting processed by an operator using specific machinery for the task. The operator’s knowledge of the process within this cell is important for providing a quality product to the next work cell. First the operator must have the material needed to complete the process within the work cell. This material can be transferred from department to department, or provided from a supplier. When the material arrives the operator must possess knowledge or be trained to operate the machinery safely for optimal output.
In most organizations the operator(s) within the work cell are familiar with the quality checks for their process. Their work gets noted on daily work orders. These work orders include information about the product specifications for the process performed in the work cell, material used, planned cycle time and due dates. Upon completion the operator must sign-off that the components were made to specification and the date and/or time completed.
In the processing the operator may be asked to do piece-part inspection on each part or randomly. The inspected work-piece will need a pass or fail identification mark. Depending on the point in production of the work-piece, or finish requirements of the work-piece simple rubber stamps or steel hand stamps might be used. For safer hand stamping operations the organization might consider a spring-loaded inspection tool.
Other times the same component is being manufactured in other work cells on the production floor. It then becomes important to identify the work cell or machine, as well as the pass/fail. Again the traditional method of stamps might be employed for marking this information. However, with multiple cells, the throughput requirements for production might demand more efficient methods of identifying the work cell. In these situations, an impact press or dot peen marking system might be the marking solution chosen. These units can communicate with other machinery in the work cell through PLC (programmable logic control) or PCs allowing the work cell to become more efficient in the component processing yielding savings over a manual marking operation.
It is important for the manufacturer to track the material for defects allowing them to work with their suppliers to correct the situation. In order to do this it is essential to find a characteristic unique to the material. As an example, for metals such as steel, the heat number for the batch of plate, bar, or round stock becomes the traceable identifier. This heat number often needs to be re-marked several times during manufacture depending on the processes in which the workpiece must pass. This means temporary and permanent marks may be required. Depending on the size and shape of the workpiece the tools chosen for this requirement can be challenging. Portable marking tools such as powder-charged or air-powered marking tools may be required. Again, the dot peen technology offers flexibility for these requirements with portable marking options in both air and electric configurations.
Date codes are another critical identifier for quality management. When organizations run several shifts, a shift identifier may be included as part of the date code. Hand-held holders with interchangeable type characters offer economical options for multiple character marking requirements. It is important to keep in mind how frequently the change of characters occurs. More frequent change-over may require a different marking technology for efficiency.
The company may be one of many sources supplying product to the customer making vendor identification important. For brand awareness companies may choose to directly apply their logo or company name. Other times the manufacturer may choose to apply a nameplate or label with their company name. Nameplates may include windows for variable text about the component such as a model number or serial number. Depending on the volume of nameplates being marked per batch the options might include hand stamps, holders with inter-changeable type, impact presses with special tooling to match the nameplate or dot peen marking systems with feeders.
Quality Management initiatives and industry demands for traceability give reason for excitement and hope. The need for marking solutions is ever-growing through industry standards. Marking equipment suppliers should take the time to become knowledgeable about the requirements of quality programs, including the marking requirements, so in turn they are prepared when chosen as the vendor partner.